Riachuelo environmental restoration system
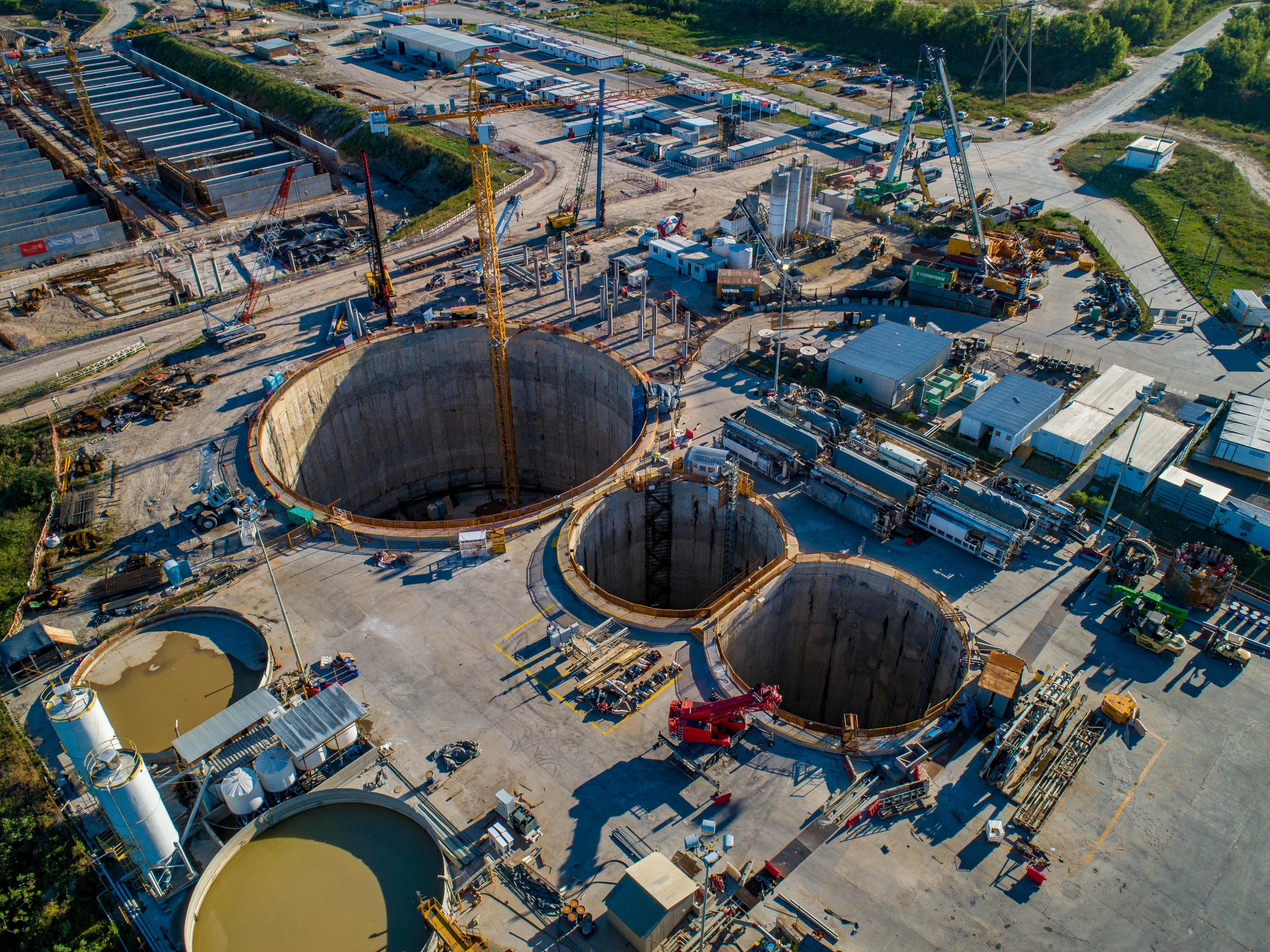
The works, contracted to a joint venture of construction companies led by Webuild, foresees the execution of a 50m deep underground chamber made from 4nr circular shafts interconnected with each other, plus a sub fluvial 4,3m ID outfall tunnel of 12km length excavated with an EPB type TBM, and 34nr vertical diffusors to be executed along the last 1,5km of the tunnel, by means of an innovative technology named “Riser Concept”.
Once completed, the overall scheme will have a strong environmental and social impact as it will help cleaning up the Matanza – Riachuelo basin which in the last decades has been affected by a massive demographic boom and more importantly by a severe number of industries disposing in uncontrolled manner of their production wastes. The scheme forms part of the broader programme for the sustainable development of the Matanza-Riachuelo basin, which is financed by the World Bank and is aimed at the environmental restoration of the whole area nowadays considered one of the worst polluted not only in Argentina but also worldwide.
On 22 November 2019, after 24 months from its commencement, the tunnel excavation works have been completed achieving with a ground cover of approximately 27m underneath the river bed the final distance of 12km from the coast, where the TBM named Beatriz will be abandoned and buried. With its 12001m of length, the tunnel already ranks as the fourth longest submarine tunnel worldwide and the third excavated with a TBM.
Hydraulic Compensation Shaft
It consists of an underground structure formed by 4nr circular shafts, made with 60m deep 1,20m thick diaphragm walls, excavated using a hydromill. The walls key into an impermeable layer of stiff marine clays allowing the safe excavation of the shaft (this was partly carried out in dry conditions and partly underwater with a dragflow). Once the excavation reached its foreseen lowest level, a concrete bottom plug was constructed adopting the “Tremie-Dobber” technology and allowing the drying out of the shaft plus construction of the permanent bottom slab and tunnel launching portal.
Outfall Tunnel
The outfall tunnel runs for its entire route under the bed of the River Plate at an approximate depth of 40m and has been excavated with only one EPB type TBM presenting a cut diameter of 5,20m. The 4,3m ID tunnel lining is made of precast concrete rings, each made from 5nr 30cm thick segments. These same segments will form the permanent lining of the tunnel which during the operation phase will act as pressure duct connecting the hydraulic compensation chamber with the river. Such demanding condition renders the tunnel one of the very few examples all over the world where the precast concrete segmental lining has been designed to resist tension forces.
Diffusion Risers
The tunnel will be connected hydraulically to the river by means of 34nr vertical risers to be executed by means of an innovative technology named “Riser Concept”. In correspondence of each diffuser, or “Riser”, a pair of special rings have been installed to allow in a second phase the vertical jacking of the Riser itself from inside the tunnel. Each Riser will be eventually formed by a series of 712mm OD Duplex stainless steel pipes, jointed with each other by bolted connections or through spigot-bell joints, and jacked for an approximate length of 27m. Once the riser top breaks through above the river bed a series of maritime works will be required to complete it with a rosette head which will allow the discharge of the treated effluent and its diffusion into the river waters.
Sustainability KPIs
KPI
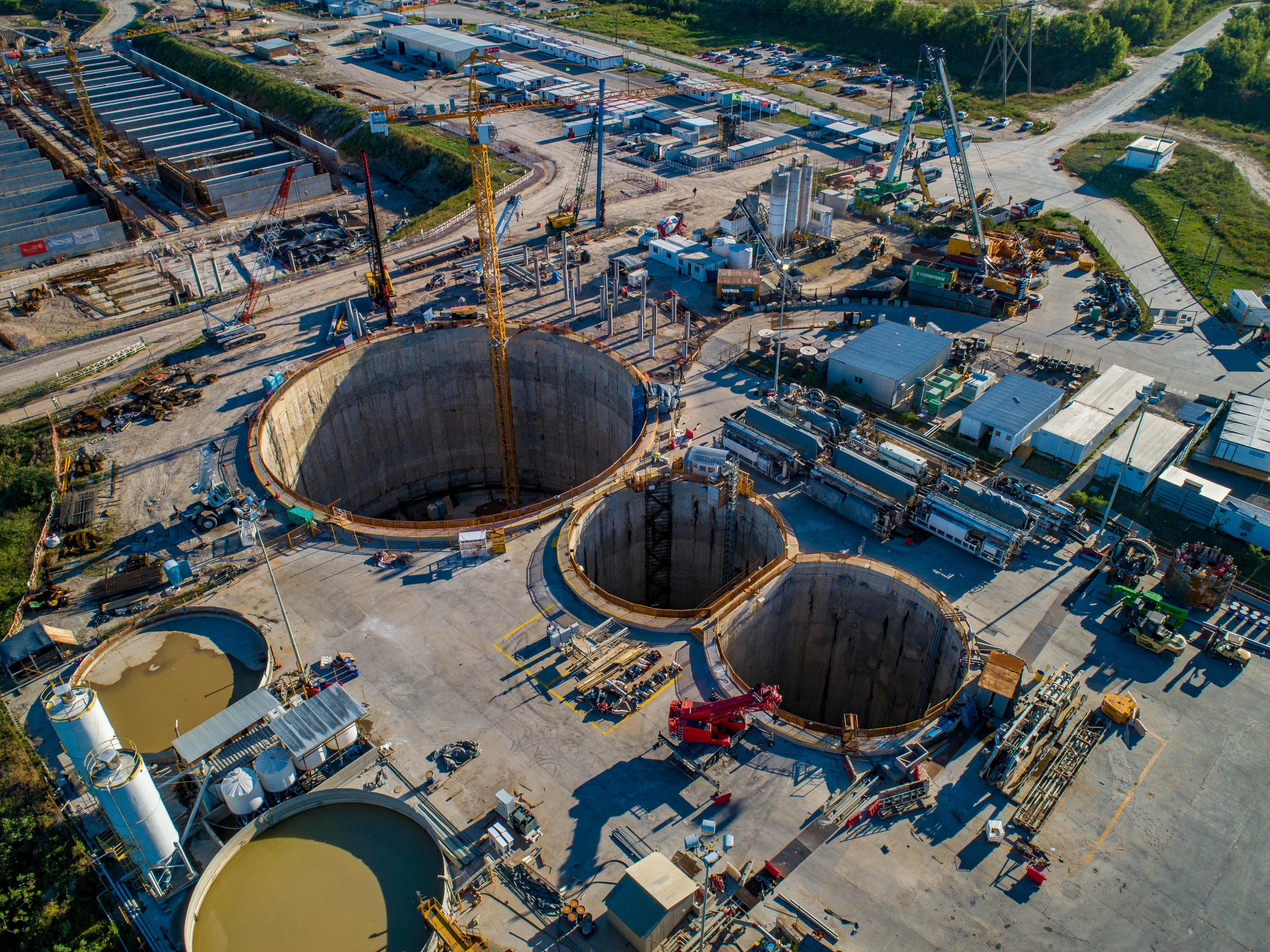
Technical data
+ + +
m³ Cleaning area
+ + +
m³ Earthmoving
+ + +
m³ Concrete